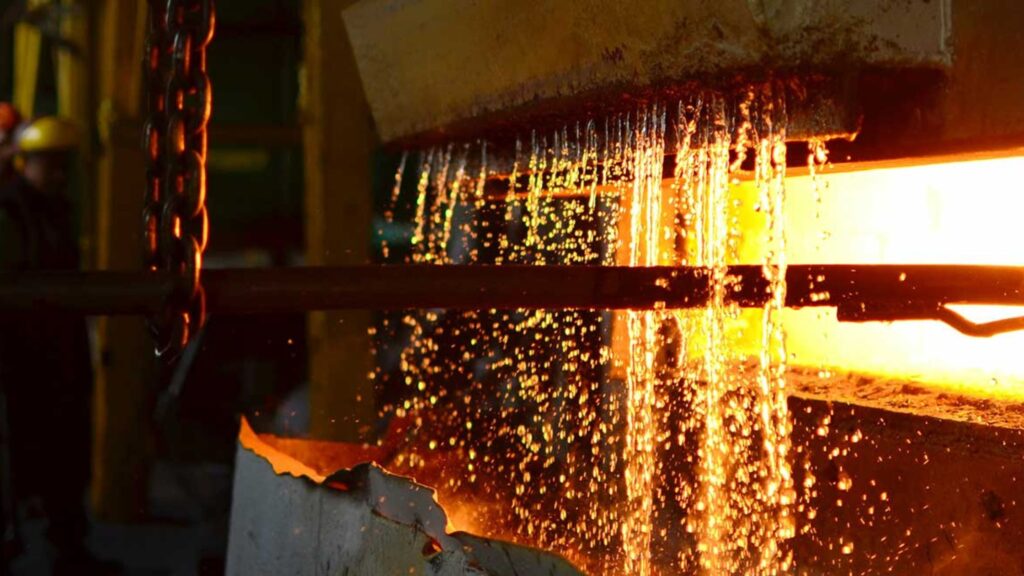
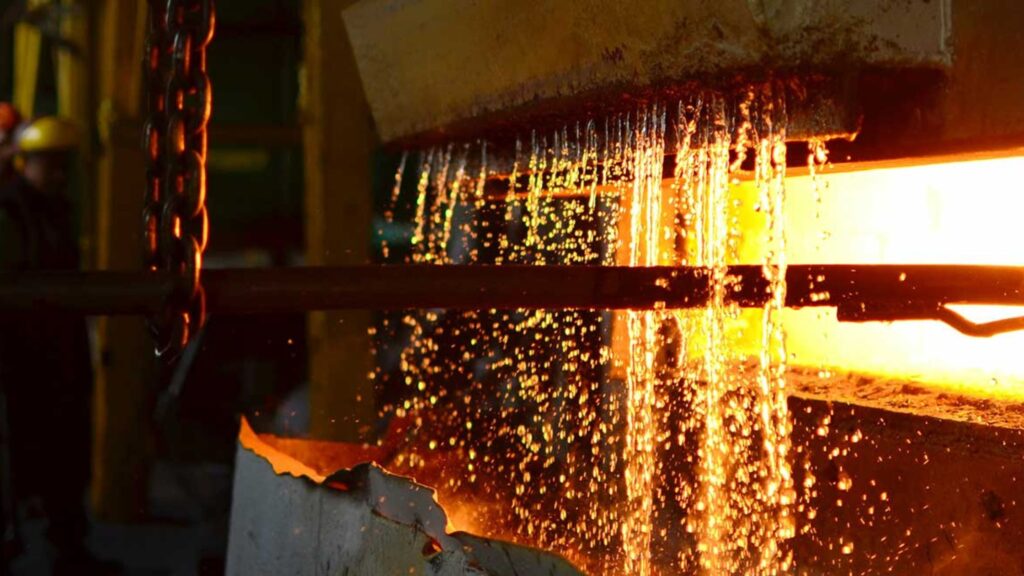
Metal hardening is one of the most critical processes in the production of small metal parts. It reduces the risk of defects or fractures and contributes to the creation of high-quality products designed to meet the demands of highly competitive industries.
While in some cases hardening is recommended, in others it is essential. In this article, we examine both scenarios, highlighting the potential benefits of this process.
What Is metal hardening?
Metal hardening is a heat treatment that increases the mechanical strength, hardness, and durability of steel. The process involves controlled heating of the material to a specific temperature, followed by rapid cooling in a medium such as oil, water, or air. This sudden temperature drop alters the internal structure of the steel, endowing it with superior mechanical properties.
In the small metal parts sector, hardening allows components to withstand high loads, resist wear, and maintain their shape under mechanical or thermal stress. Screws, pins, springs, and other critical elements benefit from hardening by extending their service life and improving performance.
Read also “Metal small parts: future perspectives”
When is metal hardening necessary?
The quench hardening process is essential for components exposed to mechanical stresses, vibrations, friction, or harsh environments. High-strength screws, pins for automotive applications, precision gears, and parts used in industrial machinery are typical examples where hardening is vital to ensure reliability and durability.
However, not all small metal parts require hardening.
For components with primarily decorative purposes or minimal mechanical loads, such as lightweight fastening accessories, hardening may not be necessary. In such cases, simpler treatments like burnishing or galvanising can improve aesthetics and corrosion resistance without significantly altering mechanical properties.
Techniques and Processes
The most commonly used hardening techniques vary according to the type of steel, part geometry, and production requirements. Here are some examples:
- Induction hardening – this method involves rapidly heating the component using induced currents, followed by immediate cooling. It is ideal for small parts requiring surface hardening while leaving the core more ductile and impact resistant.
- Oil quenching – one of the most widespread techniques, this involves immersing the heated part in an oil bath. This method ensures controlled cooling, minimizing the risk of distortion and cracking, making it particularly suitable for complex parts or those with tight tolerances.
- Water quenching – used when very high hardness is required, this technique offers rapid cooling but carries a higher risk of distortion. It is suitable for simple components or for certain steels designed to withstand abrupt temperature changes.
- Controlled atmosphere hardening – this process is conducted in oxygen-free furnaces, preventing oxidation and ensuring a high-quality surface finish. It is essential for precision parts used in critical industries such as aerospace and medical devices.
Read also “The state of the art of CNC machining”
Challenges in metal hardening: risks and how to avoid them
Despite its importance, metal hardening presents challenges that, if not properly managed, can compromise component quality. Common issues include deformation, cracking, and loss of ductility.
Deformations occur when cooling is uneven, leading to undesirable dimensional changes, particularly critical in small metal parts with tight tolerances. To prevent this, it’s crucial to select the appropriate cooling medium (oil, water, or air) and carefully monitor cooling rates. The use of temperature-controlled furnaces and techniques like protective atmosphere hardening also reduces deformation risks.
Cracking can result from high thermal stresses during rapid cooling. To mitigate this, it’s advisable to use steels with good hardenability and implement a preheating stage to minimize thermal differences between the part’s surface and core.
Loss of ductility makes components brittle and prone to sudden failure. In this case, applying a tempering treatment after hardening restores a balance between hardness and toughness.
Relying on a specialized company for heat treatments ensures precise control of each hardening phase, minimizing risks. Expertise and advanced technology guarantee products that meet technical specifications, offering high reliability and performance.