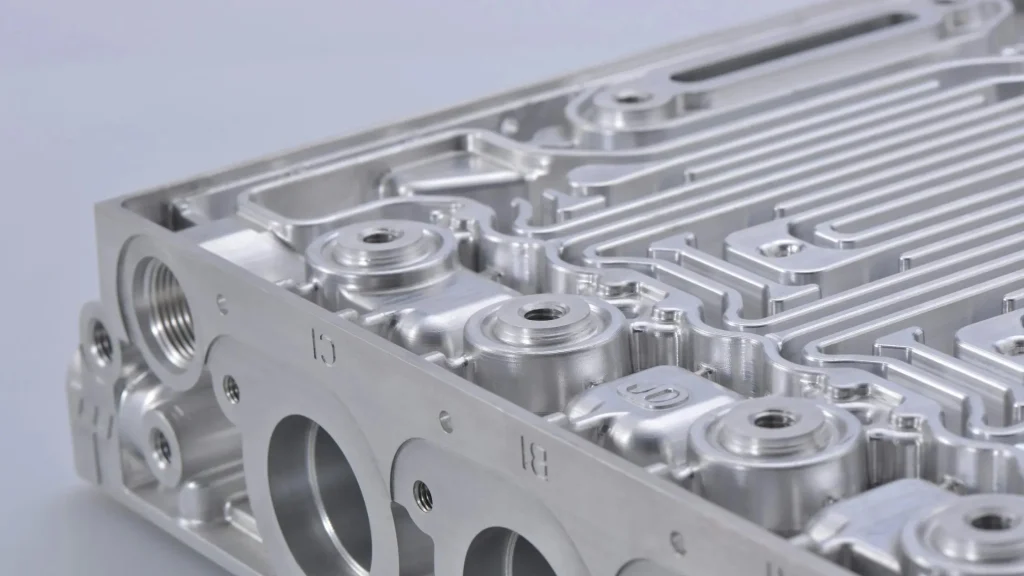
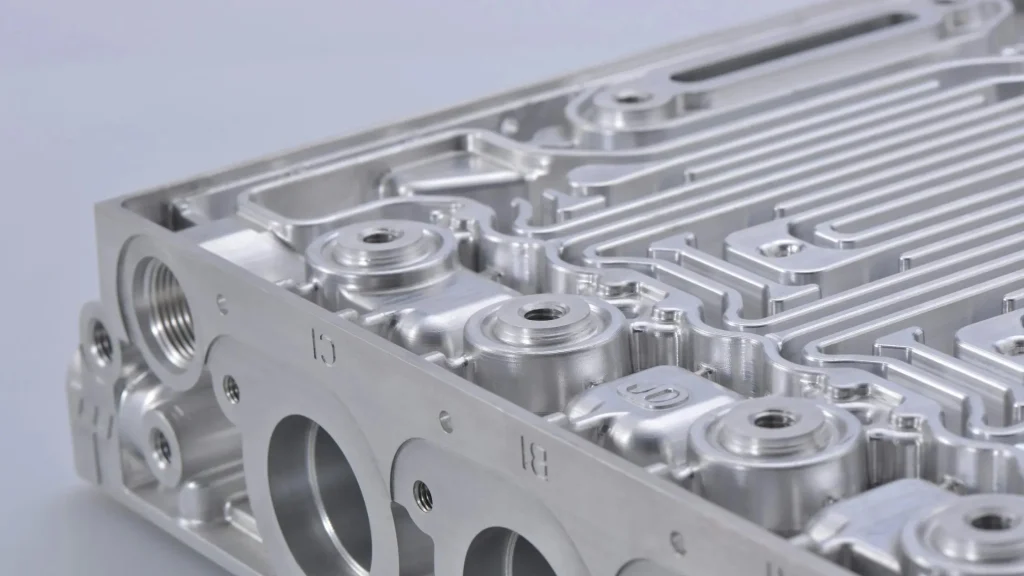
When we talk about CNC machining, we are referring to a key element in the production of components with high standards of quality and accuracy, with applications in industries ranging from aerospace, automotive, medicine, and watchmaking, where even small changes in dimensions can compromise function.
In an increasingly demanding industrial market, for all companies that make innovation and competitiveness their strengths precision machining is an essential requirement.
This article aims to define and list some of the main notions on the subject.
CNC machining techniques
In the roster of precision machining, there are multiple possibilities and variations. The main ones are shown below.
- Turning is a technique that uses a tool to remove material from a rotating piece; it is ideal for making axes, pivots, and precise cylindrical surfaces.
- Galvanization is a process in which a metal object is coated with a layer of zinc, usually by dipping or spraying, to prevent corrosion.
- Rectification is used to achieve extremely smooth surface finishes and very tight dimensional tolerances, particularly important for parts with complex geometries.
- Tumbling is a mechanical process involving removing excess materials from a metal surface by using specific tools, such as milling cutters or lathes, to obtain precise shapes.
- Other techniques include drilling, EDM (electrical discharge machining) to machine hard materials such as hardened steel and the laser cutting for precision and speed in machining on metallic and non-metallic materials.
The choice of the technique depends on the specifications of the part to be made, the materials used and the tolerances required.
Materials and tolerances
In precision machining processes, the choice of materials plays a crucial role. Materials such as stainless steel, aluminium, special alloys, and composite materials are selected based on the desired properties of the final component. Stainless steel, for instance, offers corrosion resistance and strength, while aluminium is lightweight and suitable for components with high thermal conductivity.
Dimensional and geometric tolerances, are critical parameters, which influence the functionality and interchangeability of components. Modern CNC technologies allow tolerances within a few microns, providing repeatable precision even for mass production.
The combination of appropriate materials, tolerances and quality control results in highly-efficient precision machining.
Quality control and certifications
Quality control is one of the main requirements for ensuring that components meet the required standards. The use of advanced tools, such as three-dimensional measuring machines, profile projectors and precision measuring instruments, allows the size, shape, and surface finish of parts to be verified with great accuracy.
Quality certifications, such as the ISO 9001 standard, attest to the strict quality control processes carried out during all stages of production and demonstrate our company’s commitment to ensuring high quality standards and satisfaction of customer requirements.
Apart from general certifications, certain sectors such as aerospace often require more rigorous certifications, such as AS9100, demonstrating compliance with industry-specific requirements.
Quality control and certifications are therefore essential to ensure the precision, reliability and regulatory compliance of the components manufactured, ensuring customer satisfaction and our company’s competitiveness in the market.
Mechanical processing and industry 4.0
The concept of industry 4.0 is often used in an abstract way, but in the case of CNC machining there are concrete applications that can greatly improve work processes.
In the context of precision machining, the use of computer numerical control (CNC) machines has become the norm, enabling automatic programming of operations, and ensuring high repeatability and precision. Connecting machines in intelligent networks enables real-time monitoring of performances, the collection of production data and process optimization.
Digital simulation and virtual prototyping make it possible to test and optimize machining processes before physical production, reducing development time and costs. Integrated quality control systems use advanced sensors and data analysis algorithms to ensure dimensional and functional conformity of components.
Industry 4.0 has the potential of making precision machining more efficient, flexible, and competitive, enabling companies to meet the growing demands for customization, quality, and reduced lead times in the global industrial landscape.
Are you looking for a team of experts on CNC machining? Look no further!
Tel.: +39 0362 335684