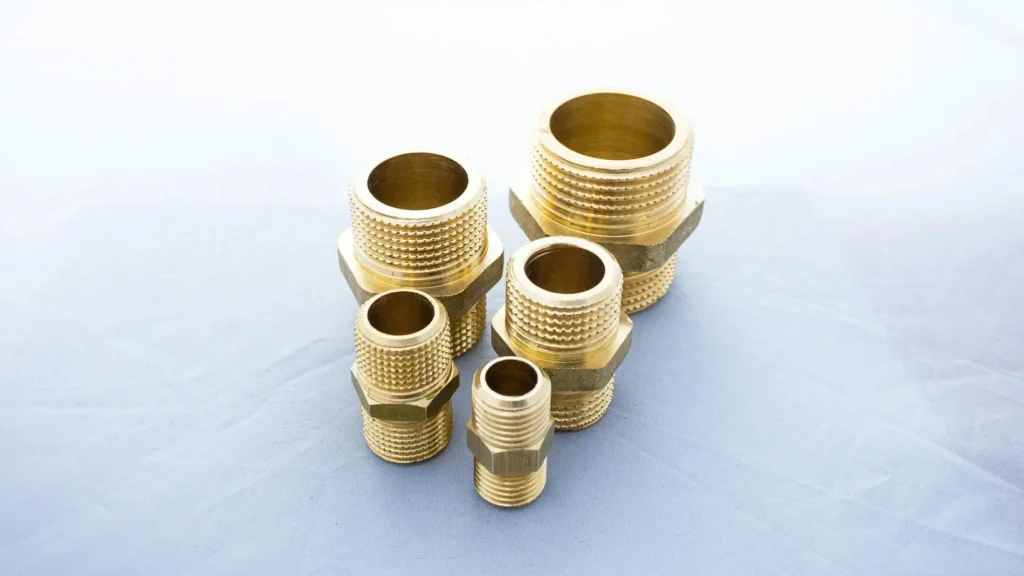
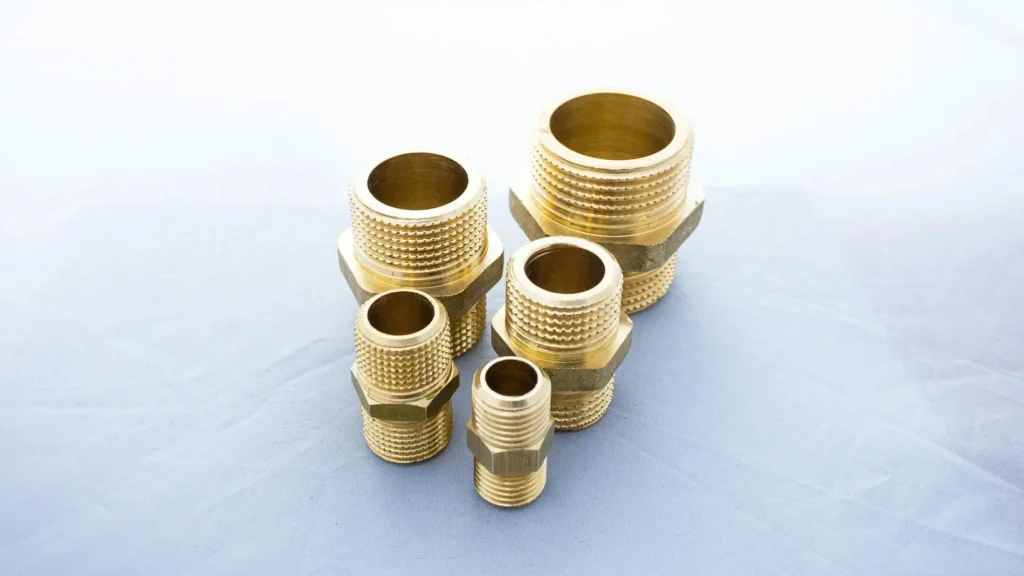
Hydraulic fittings are integral parts of the operation of machinery and systems that businesses and individuals use every day. These items are used to connect, branch, and terminate pipelines and tubes, and boost the efficiency and safety standards of all equipment that carries high-pressure fluids, such as water, oils, and gases.
In this article we provide answers to some of the most frequently asked questions on the topic.
What is the purpose of hydraulic fittings?
The purpose of hydraulic fittings is to provide structural and functional integrity of hydraulic systems, to prevent fluid leaks, to prevent damage to structures, and to prevent system malfunctions.
Apart from connecting piping, they also allow for branching out and terminating flow lines. Adaptable to specific project requirements, they provide proper distribution of fluids within the system.
There are countless types of hydraulic fittings and materials available for making them. This makes it possible to adapt to the needs of various industrial, commercial, and domestic applications.
What are the main types of hydraulic fittings?
There are mainly two types of fittings: threaded fittings and press-fit fittings.
Threaded fittings, which are more common, are used with a layer of insulation (hemp or Teflon) to connect metal pipes via internal or external threads, and provide a secure connection without using specialized tools.
On the other hand, press-fit fittings are used to connect rigid pipes by means of a compression ring which provides sealing and pressure resistance. These fittings are installed using special press clamps and are used when there is a need for reliable connections without using any insulation.
The choice of fitting type depends on a variety of factors, including the specifications of the application, operating pressure, and pipe material.
What differences are there between brass, stainless steel and plastic fittings?
The main differences between brass, stainless steel, and plastic hydraulic fittings are physical properties, performance, and specific application in hydraulic systems.
- Brass fitting: known for its resistance to corrosion and deformation, it is suitable for applications requiring good mechanical strength and durability. It is often used in residential and industrial hydraulic systems.
- Stainless steel: a steel fitting offers superior corrosion resistance compared to brass and is well suited for harsh environments and those exposed to dampness. It is used in sectors such as the food, chemical and shipbuilding industries.
- Plastic: hydraulic fittings made of materials such as polypropylene and PVC, are lightweight, inexpensive, and resistant to chemical corrosion, but may have limitations related to pressure and temperature. They are commonly used in residential hydraulic, irrigation and drainage systems.
Each material has advantages and disadvantages related to working conditions, compatibility with the transported fluid, and specific needs of application.
How important are certifications?
As it is easy to guess, the quality of metal fittings – in terms of safety, reliability, and performance of hydraulic systems – is intertwined with the quality of the materials involved.
Fittings must comply with strict regulations and quality standards, such as ISO 9001 certifications for the quality management system and material-specific certifications, such as DIN, ASTM, ANSI and other international standards. In the case of fittings manufactured for the food industry, it is also necessary to have a MOCA certification.
These certifications ensure that the materials used are suitable for the intended use, can withstand stress, and maintain their properties over time, while ensuring safe and efficient operation.
What differences are there among hydraulic fittings for domestic, industrial, and commercial systems?
The choice of fittings depends firstly on where it is going to be used, and considers the different requirements and specific operating conditions.
In domestic hydraulic systems, fittings are often small and made of materials such as PVC or polypropylene, which are excellent for withstanding the temperatures and pressures normally used in homes. Connections are usually standardized and designed to make installation by non-professionals easier.
In industrial environments, fittings must withstand more severe conditions, such as extreme temperatures, chemicals, and high pressures. Materials such as stainless steel and special alloys provide strength and durability in these settings, with fittings designed for complex and critical systems.
In the business sectors, fittings must combine robustness and ease of maintenance, as they are often used in systems that serve the public at large. The materials and fittings chosen depends on where they will be installed, such as at restaurants, hotels, hospitals, and shopping malls, each with special requirements for fluidity, hygiene, and reliability.
Are you looking for a team of experts in the production of metal fittings? Look no further!
Tel.: +39 0362 335684